[ad_1]
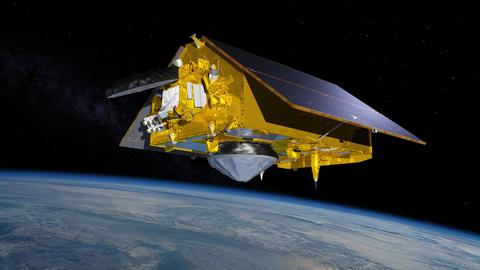
Credit:
NASA Jet Propulsion Laboratory
Many satellites perform very important and profitable tasks, but some may be deactivated with fuel still in the tank due to current methods of measuring the amount of fuel. More accurate fuel gauges could help ensure satellites stay operational longer and time in orbit is longer.
Liquids don’t perform as well in space as they do on Earth. Inside a spacecraft, microgravity allows liquids to glide and float freely.
This behavior has made it difficult to define the amount of fuel in satellites, but a new fuel gauge prototype designed at the National Institute of Standards and Technology (NIST) could offer an ideal solution. The indicator, described in the Journal of Spacecraft and Rockets, can digitally recreate the 3D shape of a fluid based on its electrical properties. The project could potentially provide satellite operators with reliable measurements that would help prevent the satellites from colliding and keep them operational longer.
“Every day a satellite stays in orbit is likely to be millions of dollars in revenue,” said Nick Dagalakis, NIST mechanical engineer and co-author of the study. “The operators want to use every drop of fuel, but not enough to empty the tank.”
Letting a satellite’s fuel tank run dry could leave it stuck in its original orbit without fuel to avoid crashing into other satellites and producing dangerous clouds of debris.
To reduce the likelihood of a collision, operators save the last few drops of fuel to eject satellites into a graveyard orbit hundreds of miles away from the working spacecraft. However, they could waste fuel in the process.
For decades, measuring fuel in space was not an exact science. One of the most frequently used methods involves estimating the amount of fuel burned with each thrust and subtracting that amount from the volume of fuel in the tank. This method is fairly accurate at first when a tank is close to full, but the error of each estimate continues on to the next, aggravating each thrust. When a tank is low, estimates become more like rough assumptions and can miss up to 10%.
Without reliable measurements, operators could send satellites with fuel still in the tank in early retirement, potentially leaving a significant amount of money on the table.
The new gauge concept – originally devised by Manohar Deshpande, a technology transfer manager at NASA’s Goddard Space Flight Center – makes use of a low-cost 3D imaging technique known as electrical capacitance volume tomography (ECVT).
Like a CT scanner, ECVT can approximate the shape of an object by taking measurements at different angles. But instead of firing X-rays, the electrodes emit electric fields and measure the object’s ability to store electric charge, or capacity.
Deshpande sought the expertise of Dagalakis and his NIST colleagues – who had prior experience in fabricating capacity-based sensors – to help make his designs a reality.
Credit:
N. Hanacek / NIST
In NIST’s Center for Nanoscale Science and Technology’s NanoFab cleanroom, the researchers produced sensor electrodes using a process called soft lithography, in which they printed ink patterns on copper foil with a flexible plastic backing. Then, a corrosive chemical sculpted the exposed copper, leaving the desired metal strips, Dagalakis said.
The team lined the inside of an egg-shaped container modeled on one of NASA’s fuel tanks with the flexible sensors. Throughout the interior of the tank, the electric fields emitted by each sensor can be received by the others. But how much of these fields end up being transmitted depends on the capacity of whatever material is inside the tank.
“If you don’t have fuel, you have the highest transmission, and if you have fuel, you will have a lower reading, because the fuel absorbs the electromagnetic wave,” Dagalakis said. “We measure the transmission difference for every possible pair of sensors and by combining all these measurements you can know where it is and there is no fuel and create a 3D image.”
To test what the new system’s fuel metering capabilities might look like in space, the researchers suspended a liquid-filled balloon in the tank, mimicking a blob of liquid in microgravity.
Many liquids commonly used to propel satellites and spacecraft, such as liquid hydrogen and hydrazine, are highly flammable in Earth’s oxygen-rich atmosphere, so the researchers decided to test something more stable, Dagalakis said.
On Deshpande’s recommendation, they filled the balloons with a heat transfer fluid – normally used to store or dissipate heat energy in industrial processes – because it closely mimicked the electrical properties of space fuel.
The researchers activated the system and sent the capacity data to a computer, which produced a series of 2D images that mapped the fluid’s position across the length of the reservoir. Once compiled, the images resulted in a 3D rendering of the balloon with a diameter that was less than 6% of the actual balloon diameter.
“This is just an experimental prototype, but this is a good place to start,” said Dagalakis.
If further developed, the ECVT system could help engineers and researchers overcome many other challenges presented by the behavior of liquid in space.
“The technology could be used to continuously monitor fluid flow in the numerous tubes aboard the International Space Station and to study how small forces of flowing fluids can alter the trajectory of spacecraft and satellites,” Deshpande said.
Document: SH Yang, YS Kim, NG Dagalakis and Y. Wang. Flexible groups of electro-capacitive tomographic volume sensors for measuring the fuel of spacecraft. Journal of Spacecraft and Rockets. Published online 11 November 2020 DOI: 10.2514 / 1.A34747
.
[ad_2]
Source link