[ad_1]
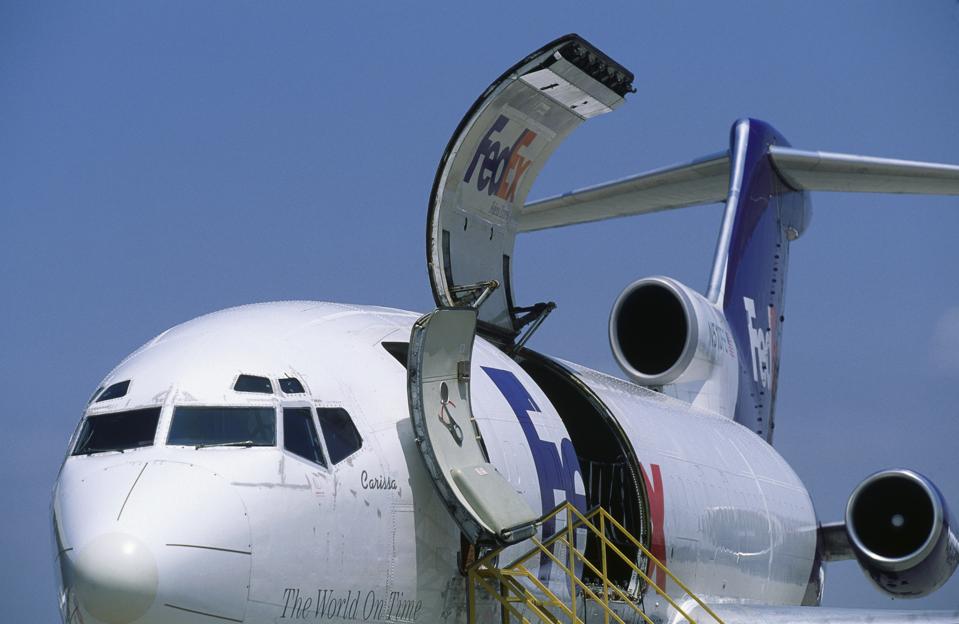
cargo door open on parked FedEx Boeing 727-100F called “Clarissa”. (Photo by: … [+]
Universal Images Group via Getty Images
While people think life is returning to normal, one of the biggest questions that still doesn’t have an answer is when will a coronavirus vaccine be ready. This will depend on when effective vaccines are available. But beyond that, there are all the supply chain obstacles associated with the production, storage, distribution and administration of vaccines.
The race to develop an approved coronavirus vaccine with more than 50 vaccines in human clinical trials and more than 85 preclinical vaccines being tested in animals. There are six stages in the development cycle to get a vaccine from the laboratory to the general public. For some of the ongoing trials, the scientists combined the steps to try to speed up the development and approval process. From a numerical point of view, 36 coronavirus vaccines are Phase 1, 14 are Phase 2, 11 are Phase 3, 6 have obtained limited approval in China and Russia.
The first phase, which focuses on preclinical testing, presents some procurement barriers for US pharmaceutical companies. In preclinical tests, scientists test a new vaccine on cells and then on animals. The United States is facing a shortage of test monkeys due to increased demand and decreased supply from China.
Distribution of the coronavirus vaccine
With so many trials underway, there are still significant barriers to getting vaccines to market. Once an effective vaccine has been approved for mass distribution, there are also a number of logistical obstacles that will need to be addressed. Therefore, logistics companies have been busy preparing for the past few months.
One problem that could slow the development and distribution of a vaccine is the shortage of glass vials. The rush to produce a vaccine has resulted in a rush to secure supplies. The problem with the glass supply chain is that the market is traditionally fixed and slowly growing. This means that it is also prone to shortcomings, such as this one. The relatively low number of glassmakers contributes to the problem. Experts fear that the lack of producers and the exponential increase in demand could lead to difficulties in producing the billions of doses of the vaccine needed.
Assuming glass makers can keep up with anticipated demand for vials, the next problem becomes creating the infrastructure to move all those vaccines around the world. Temperature control is of utmost importance for the vaccine, as it will need to be stored at temperatures around – 94 Fahrenheit. Both UPS and FedEx
FDX
UPS built two cold storage rooms in Louisville, KY and the Netherlands near the company’s air hubs. The two sites should help ensure the global distribution of a vaccine once it becomes available. Each facility will house 600 deep freezers that can hold 48,000 vials of the vaccine at temperatures as low as -112 Fahrenheit. Between the two facilities, UPS will be able to store over 57 million doses of the vaccine.
FedEx began building its freezer infrastructure nearly ten years ago in response to the H1N1 outbreak. FedEx now has nearly 90 cold chain facilities around the world where vaccines can be safely stored. The company has also started using Bluetooth to broadcast a location every few seconds. Combined with temperature sensors, if something goes wrong with a shipment, FedEx will be able to pinpoint its location and work to fix the problem quickly.
Pfizer
PFE
Maersk has signed an agreement with COVAXX to ship the US pharmaceutical company’s Covid-19 vaccine around the world when and if it gets regulatory approval. COVAXX is currently in Phase 1 of its vaccine trial in Taiwan and will launch Phase 2 in the United States as part of a partnership with the University of Nebraska Medical Center. COVAXX will also conduct a large-scale human efficacy clinical trial in Brazil. Maersk will oversee all logistical activities to ensure efficient transportation to developing countries. The agreement includes end-to-end supply chain management, packaging and shipping, by air or sea, ground transportation, storage and warehouse distribution to facilities to support COVAXX’s requirements for a supply chain at controlled temperature of pharmaceutical grade. COVAXX plans to produce 100 million doses of its vaccine in early 2021 and one billion doses by the end of 2021.
Then there are the obstacles to production. Pharmaceutical companies are subject to GMP (Good Manufacturing Practice) regulations. GMP is a system to ensure that products are constantly produced and checked according to quality standards.
Additionally, pharmaceutical manufacturers point out that the labeling documentation produced for new drugs creates supply chain barriers that are not insignificant. Packaging and inserts must be approved by each country. This means that instead of producing a global storage unit, each nation requires a separate SKU. This proliferation of SKUs means that documentation often delays launches in one country or another. Some drug companies have responded by manufacturing the drugs in one place and then shipping them in bulk to a specialized packaging partner who can respond quickly to these requests. Then the finished products are shipped from the packaging partner’s facility into the global market. In short, an extra logistical leg is often needed for pharmaceutical supply chains.
Finally, the development of the COVID supply chain is likely to negatively impact other supply chains. Getting the vaccine to be distributed will require herculean efforts never seen before. This, in turn, will impact the overall air cargo. Cargo carriers will likely slam more shipments in favor of distributing a coronavirus vaccine. This could cause delays in shipments as a shortage of available air transport capacity is foreseeable. But in the interest of the common good, delays in consumer goods can certainly be forgiven.
The lead author of this article was Chris Cunnane.
.
[ad_2]
Source link